ABOUT US
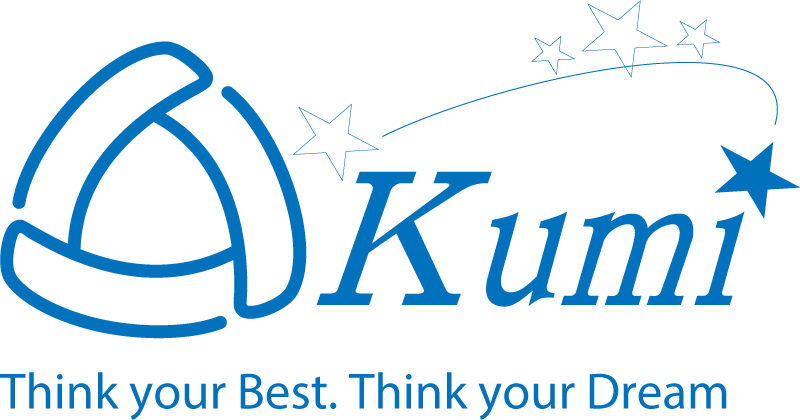
We support the cutomer's supply chain
with the reliable technic and the solid production system
We expand the bussiness of R&D for resin and rubber parts, designing, manufacturing and sales totally, especially the automobile interior & exterior parts.
We will show our expertise in the technical fields of thermoforming felt and resin injection molding and also respond to meet the request for weight saving and highly rigidity.
We continue strengthening the quality assurance and the production system to carry out our responsibility as a company forming customers' supply chain.
We propose the charming products and technology to the automobile manufacturing companies around the world
and also to the customers other than automobile industry by improving our original technology including 「KISS molding」.
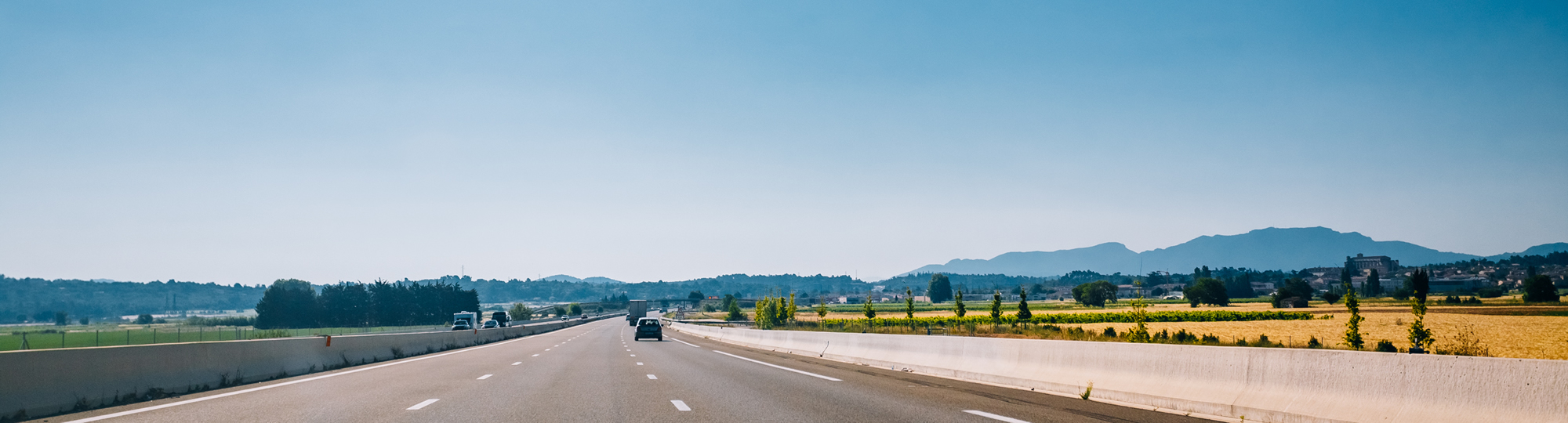
- Development
- Technology
- Production
- Quality
-
Development
Aiming for development that continues to propose new technologies and new products to customers all over the world
-
01 Market research
Based on global information gathering and market research, we will decide the concept of products to propose for the next model.
-
02 Planning
We plan the product development based on the concept.
It is about five years before the target model is released at this point. -
03 Advanced development
We start advance development based on the plan.
We develop it simultaneously in each country utilizing Kumi / Global Network.
In addition, we are using CAE (computer simulation) technology to improve efficiency. -
04 Performance evaluation
Perform various performance evaluation tests.
We conduct more severe tests assuming harsh operating environments so that users can use products with confidence.
Many of the target requirements of new technology will be discussed with customers from this time. -
05 Proposal to customers
advance development is completed, we will present to customers that they will pass the internal evaluation.
-
-
Kumi Kasei’s TechnologyWe have various technologies in injection molding and thermoformed felt.
Thermoformed felt
Achieving light weight high stiffness and unique added value globally with leading times
Weight reduction of automotive parts has been constantly being sought as a major purpose for improving fuel comsuption.
From now on, the importance of this technology is increasing as it contributes to extending the cruising distance.
In order to respond to this need, we have developed our own lightweight felt material and are offering it to the market through a production line that automates from raw fabric input to molding and trimming.
This line is a process that also takes into consideration the environment where the original raw material produced in production is converted into a solid fuel (RPF) in the company and it is not discarded.
The felt material to be used is procured in the country where the product is produced basically. Currently we procure in Japan, North America, China, Thailand and India.
We are volatilizing the raw felt film in order to keep the same performance and quality in each country’s manufacturing environment which varies from country to country, such as availability of raw materials and limitation of production facilities.
We combine a wide range of know-how such as fiber composition and molding conditions that maintains stiffness, fiber structure and original fabric structure that enhances sound absorption and shielding characteristics, raw materials that satisfy water repellent performance and chemical resistance, and surface treatment, etc.
And we produce the best raw material within the conditions that each country can have.
These know-how are also effective for improving raw fabric performance.
For example, we can supply products with unique added value such as multilayer structure that enhances soundproofing performance, global water repellent formulation that can be deployed globally.Resin injection molding
Pursuing customer’s universal needs, weight saving and high design
-
・Thin wall molding
We are promoting thinning mainly for large-sized parts with a large weight reduction effect.
We realize appearance quality without gloss even with t1.8 or less by using CAE to realize precisely the gate placement and injection control etc. precisely designed in mold and mass production condition. -
・Foam molding
Foam injection molding is applied to parts which are particularly required for light weight and high stiffness.
We have realized products with excellent product surface quality and uniform foam layer with actual magnification of 2 or more with original foaming material and molding technology without gloss unevenness. -
・Gas assist molding
It is a molding method that injects gas synchronously with resin injection to form a hollow cross section.
We are applying to the pillar garnish etc. integrating the grab rail and the grip.
This technology is used for nearly all kinds of our production to grab rails, with annual production of more than 15 million. -
・Epidermal insert molding
This technology is applied to what is required for higher appearance productivity, such as for luxury cars.
In injection molding, a skin material such as tricot fabric or nonwoven fabric is inserted into a mold,It is technology to simultaneously shape.
We mainly apply to pillar garnish. -
・KISS molding(Abbreviation for Kumi Injection Sinkmarkless System, trademark registration No. 5758963)
It is our unique sink markless molding method. It is a molding method that does not precipitate the influence of volumetric shrinkage of the material resin which occurs in the cooling process of the injection cycle which the resin injection molding predestination has, on the product surface. We devised each of the product design, molding conditions, mold design,It is realized by fusing. Without concern for sink marks on the product surface, we can freely design the back side structure such as reinforcing ribs and mounting. (Depending on the conditions, ribs thicker than the plate thickness are also possible) In addition, because it maintains adhesion to the mold surface through the cooling process, it has very high transferability and is a technology that is good at reproducing high gloss appearance. For piano black parts, the surface appearance quality is better than painted finish without painting. Furthermore, this technology contributes to improving the impact resistance of products using materials with low impact resistance, such as acrylic, from characteristics with little residual molding strain.
-
-
Production system
Production site constantly aware of improvement
We produce plastic products for car interior and exterior parts, aiming to improve customer satisfaction.Injection molding machine General · thin wall · gas INJ etc. We have developed various types and small lot production with efficient production method suitable for purpose.
We have 13 molding machines from 2,500 t to 110 t.Hot press molding machine Form the felt material used for the trunk side with a press machine and trim it by the water-jet process.
We are promoting weight saving by combining with injection molded parts.AGV automatic transportation system Move the hot press molded product to the next process.
It is a system that automates the movement between processes.Assembly robot Identify the product from the identification tag QR code and automate various assemblies and camera assembly inspections.
We have two large robots and two small robots.Assembly / inspection line We will assemble the components we have under control of automatic weighing flexibly according to customer’s order.
We guarantee the important parts with QA machine. We are holding the assembly 23 line and inspection 9 line.-
Injection molding machine
- General · thin wall · gas INJ etc. We have developed various types and small lot production with efficient production method suitable for purpose.
- We have 13 molding machines from 2,500 t to 110 t.
-
Hot press molding machine
- Form the felt material used for the trunk side with a press machine and trim it by the water-jet process.
- We are promoting weight saving by combining with injection molded parts.
-
AGV automatic transportation system
- Move the hot press molded product to the next process.
- It is a system that automates the movement between processes.
-
Assembly robot
- Identify the product from the identification tag QR code and automate various assemblies and camera assembly inspections.
- We have two large robots and two small robots.
-
Assembly / inspection line
- We will assemble the components we have under control of automatic weighing flexibly according to customer’s order.
- We guarantee the important parts with QA machine. We are holding the assembly 23 line and inspection 9 line.
-
-
Quality Assurance System
In order to further strengthen the standardization of all operations, we also work to promote business with quality awareness by each employee, to acquire the certification of the ISO 9001 version 2015 ahead of other companies.
-
We aim to become a company that is needed by customers, develop a new model with Q (quality) C (cost) D (development) D (delivery date) M (management) as the horizontal plane, Until every moment, while evaluating the process of sales – development – mass production preparation, we have endeavored to prevent the occurrence of troubles in mass production by repeating full quality ripening.
-
Automotive is the mobility of human-centered, environmental impact must be small and absolutely safe vehicle as much as possible, the environment surrounding also continues to change from moment to moment.
As a result, safety is confirmed for each one of parts we deliver, Demands are also becoming increasingly stringent.
In order to respond to these changes with speed, we actively promoted the introduction of QA machines from the viewpoint of warranty for one finished car, thereby eliminating safety hindrance factors and ensuring one part warranty I made it.
Even in the stricter regulations on chemical substances, we are quickly grasping future changes in the situation quickly and accurately, and we are strengthening ourselves so that we can hit the first without waiting for customers to transmit.
We will continue to constantly strive to constantly strive for high antennae and to receive greater trust from customers. -
・State-of-the-art assembly automatic machine
This machine automatically welds up to the specified position and automatically inspect welding accuracy and other assy parts.
It is manufactured by KMA and has an interlock mechanism.
-
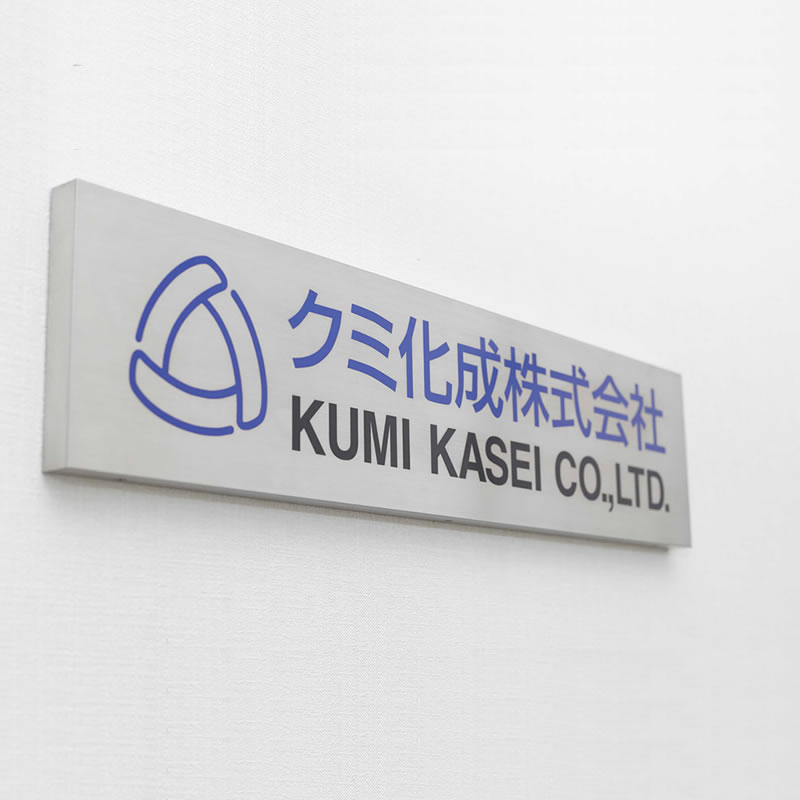
Company
Information on company information and bases around the world. We will respond to customer requests by utilizing our domestic and overseas networks.
READ MORE »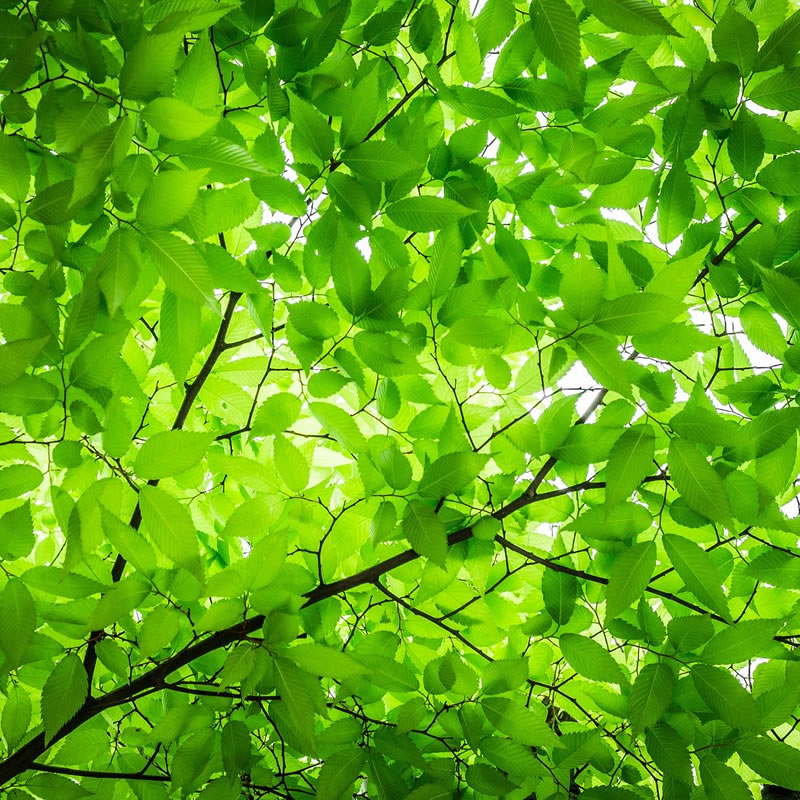
CSR
Aiming to be a company needed by society, we are working on "sustainable manufacturing".
READ MORE »